Exploring the World of Pressure Die Casting Components
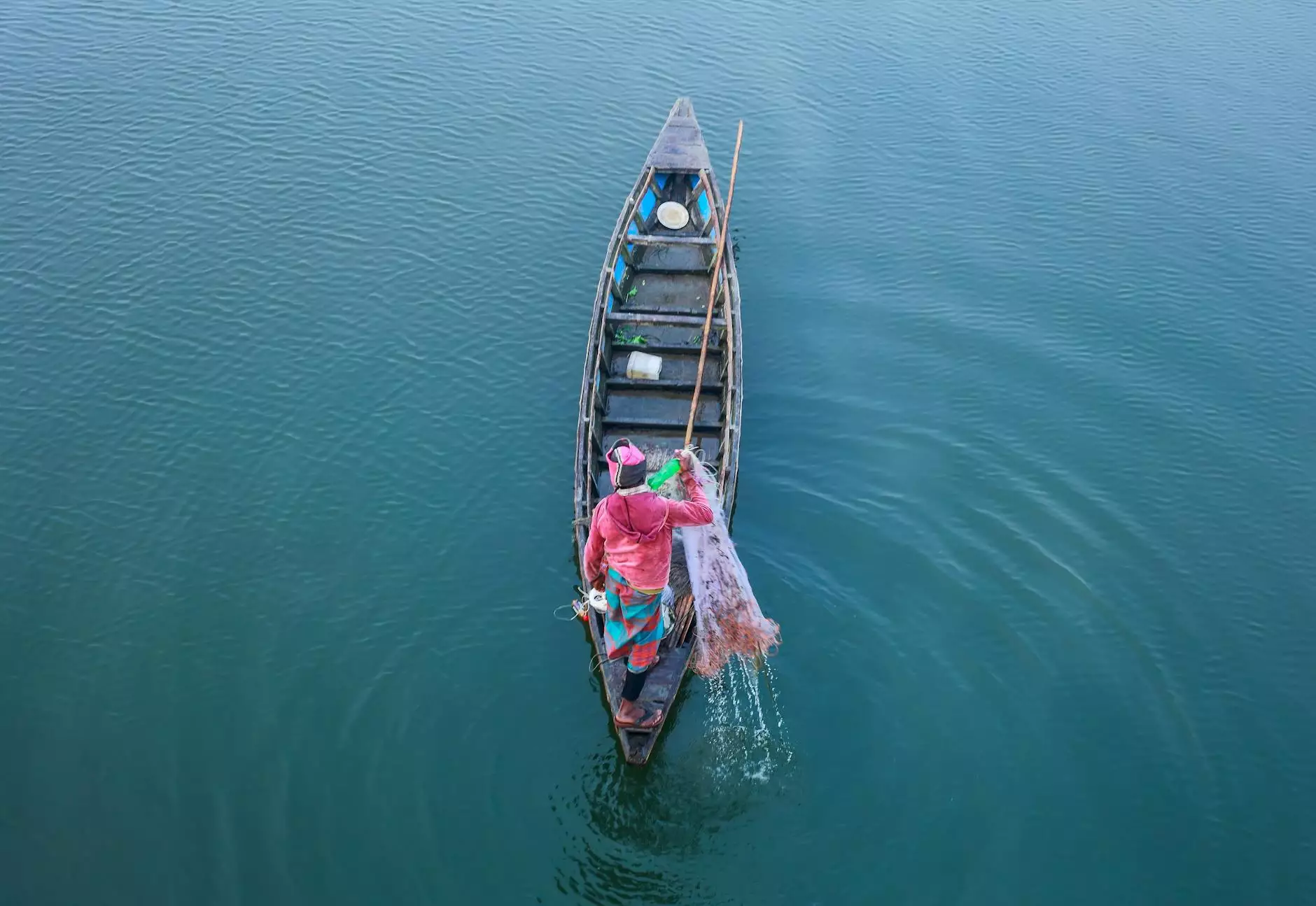
In today's industrial landscape, pressure die casting components play a pivotal role across an array of sectors. Manufacturing processes depend heavily on precise and high-quality components, making understanding pressure die casting paramount for any business involved in metal fabrication. This article will delve into the mechanisms, applications, and advantages of pressure die casting, equipping you with essential knowledge about this crucial manufacturing process.
What is Pressure Die Casting?
Pressure die casting, also known as high-pressure die casting, is a metal casting process that involves forcing molten metal under high pressure into a mold cavity. This process is particularly favored for its ability to produce complex shapes with exceptional dimensional accuracy. Here’s an in-depth look at the process:
The Die Casting Process
- Preparation: The process begins with the preparation of the die, which is usually made of durable steel that can withstand high temperatures and pressures.
- Melting: The chosen alloy is melted in a furnace. Common metals used include aluminum, zinc, magnesium, and copper.
- Injection: The molten metal is injected into the die at high velocity and pressure.
- Cooling: Once the cavity is filled, the metal is allowed to cool, solidifying into the desired shape.
- Ejection: The die opens, and the finished component is ejected from the mold.
Advantages of Pressure Die Casting Components
The adoption of pressure die casting components within manufacturing processes brings forth numerous advantages. Here are some of the key benefits:
- High Dimensional Accuracy: Pressure die casting produces components with minimal tolerances, ensuring high precision that is often required in industries such as automotive and aerospace.
- Complex Geometries: The versatility of die casting allows for intricate designs and complex shapes that would be difficult or impossible to achieve with other methods.
- Economical for Large Production Runs: Once the die is made, the cost per unit decreases significantly with production scale, making it economically viable for large quantities.
- Superior Finish Quality: Components produced through pressure die casting typically require less machining and finishing work, leading to cost savings and shorter production times.
- Material Conservation: The process minimizes waste material, resulting in more efficient resource usage.
Applications of Pressure Die Casting Components
Pressure die casting components find utility in a diverse range of industries. Let's discuss some of the prominent applications:
1. Automotive Industry
The automotive sector significantly benefits from pressure die casting, as it allows for the production of lightweight yet durable components. Common applications include:
- Engine blocks
- Transmission cases
- Housings for various assemblies
2. Aerospace Industry
Aerospace applications demand high strength-to-weight ratios, making pressure die casting a preferred choice for producing components such as:
- Brackets
- Structural frames
- Engine components
3. Electronics and Electrical Equipment
The electronics industry utilizes pressure die casting for manufacturing parts like:
- Casings for laptops and computers
- Components for electronic devices
- Heat sinks
4. Household Appliances
Many household appliances employ die casting components, enhancing their durability and aesthetics. Common examples include:
- Electric shavers
- Kitchen tools and gadgets
- Vehicle and appliance components
Comparing Pressure Die Casting with Other Methods
To fully appreciate the advantages of pressure die casting components, it’s beneficial to compare this method with other casting processes like sand casting and investment casting.
Pressure Die Casting vs. Sand Casting
While sand casting is known for its ability to produce large, simple shapes, it often results in higher tolerance levels and surface imperfections. Pressure die casting, on the other hand, excels in:
- Production of complex geometries
- Higher surface quality
- Reduced waste
Pressure Die Casting vs. Investment Casting
Investment casting is renowned for its high precision and versatility but generally has a higher cost associated with the detailed mold-making process. In contrast, pressure die casting offers:
- Faster production times
- Lower per-unit costs for mass production
- Significant reduction in material waste
Choosing the Right Metal Fabricator for Pressure Die Casting Components
With an understanding of the benefits and applications of pressure die casting components, selecting the right metal fabricator becomes critical. Here are some essential considerations:
1. Experience and Expertise
Choose a fabricator with a strong background in die casting and proven experience in various industries. A knowledgeable team can handle challenges and ensure your project meets specifications.
2. Quality Assurance
The quality of components produced is crucial. Ensure your prospective fabricator adheres to strict quality control measures and industry standards, like ISO certifications.
3. Technological Capabilities
Look for modern facilities equipped with advanced technologies for pressure die casting. This includes automated processes, CNC machining capabilities, and a robust design and development process.
4. Customer Service
Strong customer support is vital throughout the production cycle. Choose a partner who communicates effectively and prioritizes your needs during and after the production process.
Conclusion
In summary, pressure die casting components are a cornerstone of modern manufacturing, providing numerous advantages that meet the rigorous demands of various industries. From automotive to aerospace, electronics to household appliances, the importance of this technology cannot be overstated. By understanding the process, benefits, and selecting a proficient metal fabricator, your business can leverage the advantages of pressure die casting components for improved production efficiency and product quality.
For more on pressure die casting components and how they can enhance your manufacturing processes, visit Deep Mould, where we're dedicated to delivering expert insights and superior quality in metal fabrication.