Precision Plastic Molding: Elevating Manufacturing Success
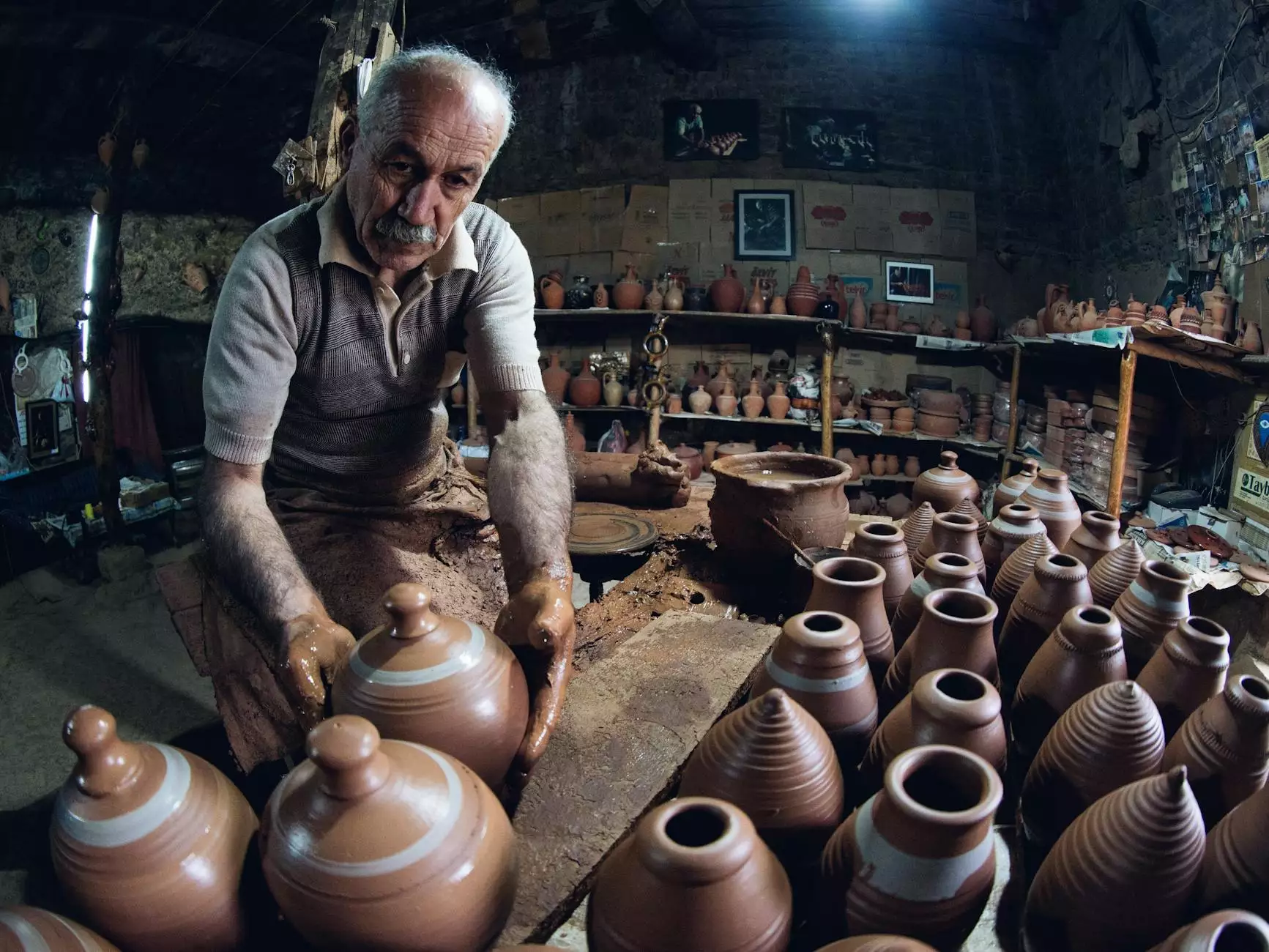
Precision plastic molding is a transformative technology that has revolutionized the manufacturing sector. Utilizing sophisticated machinery and meticulous designs, this technique allows businesses to produce high-quality, intricate components that meet stringent specifications. In a world where efficiency and precision are paramount, understanding the nuances of precision plastic molding can provide businesses a vital competitive edge.
Understanding Precision Plastic Molding
At its core, precision plastic molding is a process that involves shaping plastic materials into precise designs using a molding technique. The process is highly controllable, allowing for the production of complex geometries and fine tolerances that are essential in various industries, from automotive to electronics. The precision achieved through this process not only enhances aesthetic appeal but also optimizes functionality.
How Precision Plastic Molding Works
The precision plastic molding process consists of several key steps:
- Material Selection: The first step involves choosing the right type of plastic polymer. This choice significantly impacts the properties of the final product.
- Design Development: Products are designed using CAD (Computer-Aided Design) software, ensuring that every detail is accounted for.
- Mold Creation: High-precision molds are crafted, often from metals like steel or aluminum, to withstand the high pressure of the molding process.
- Injection Molding Process: The chosen plastic is heated until molten and injected into the mold under high pressure, allowing it to take the precise shape.
- Cooling and Ejection: After sufficient cooling, the mold is opened, and the finished parts are ejected.
- Finishing Touches: Finally, the parts may undergo secondary processes such as trimming, painting, or assembling.
Advantages of Precision Plastic Molding
Implementing precision plastic molding in manufacturing furnishes several advantages:
- High Precision and Consistency: This technique ensures that every part produced meets exact specifications, which is critical for applications requiring tight tolerances.
- Increased Efficiency: Automation in the molding process minimizes manual intervention, resulting in shorter production cycles and reduced labor costs.
- Cost-Effectiveness: While the initial setup can be capital-intensive, the ability to produce large quantities with minimal defects leads to lower per-unit costs.
- Versatility: Precision plastic molding can be utilized across various industries, accommodating a diverse range of materials and designs.
- Enhanced Product Performance: Products made through this process often exhibit superior strength, durability, and lightweight characteristics, crucial for high-performance applications.
Applications of Precision Plastic Molding
The versatility of precision plastic molding allows it to be applied across numerous sectors:
1. Automotive Industry
In the automotive industry, components such as dashboards, panels, and small precision parts are manufactured using this technology. The high precision ensures that all parts fit together seamlessly, affecting vehicle performance and safety.
2. Electronics Manufacturing
Electronics rely heavily on precise components. From casings to connectors, the precision offered through molding allows for intricate designs that support the functionality of electronic devices.
3. Medical Devices
Medical devices require the utmost precision due to strict regulatory standards. Precision plastic molding plays a significant role in producing components for instruments, implants, and disposables, ensuring safety and reliability.
4. Consumer Products
From toys to household appliances, many consumer goods benefit from precision molding. This method allows for aesthetic designs while maintaining the necessary durability.
Choosing the Right Partner for Precision Plastic Molding
For businesses looking to harness the benefits of precision plastic molding, selecting the right manufacturing partner is crucial. Here are several factors to consider:
- Experience and Specialization: Look for companies that have a proven track record in your specific industry.
- Technological Capability: Ensure that the partner uses the latest molding technologies and equipment for optimal results.
- Quality Control Processes: A robust quality assurance system is vital to maintain the high standards expected in precision molding.
- Customer Support: Choose a partner that offers excellent customer service and support throughout the development and production processes.
- Scalability: As your business grows, your manufacturing needs may change. Your partner should be able to scale up production when necessary.
Investing in Future Technologies
The future of precision plastic molding is promising, with technological advancements constantly emerging. Innovations such as the use of artificial intelligence (AI) in design and production processes are streamlining manufacturing. This not only reduces waste but also enhances efficiency and precision.
Additionally, the integration of sustainable practices in plastic production is becoming increasingly important. Manufacturers are focusing on creating biodegradable options and utilizing recycled materials to meet strict environmental standards. This not only helps the planet but also appeals to the growing consumer demand for sustainable products.
Conclusion
In summary, precision plastic molding is a cornerstone of modern manufacturing, offering numerous benefits that can significantly impact a business's bottom line. With its ability to produce high-quality, precise components efficiently, it serves as an invaluable resource for industries ranging from automotive to medical devices.
By understanding the intricacies of this technology and selecting the right manufacturing partners, businesses can leverage precision plastic molding to innovate and excel in their respective markets. As the industry continues to evolve, those who embrace these advancements will be better positioned to meet future challenges and capitalize on emerging opportunities.
For more information on precision plastic molding and to explore how partnering with experienced fabricators can enhance your manufacturing capabilities, visit Deep Mould.