The Impact of Earthquake Simulators on 3D Printing Technology
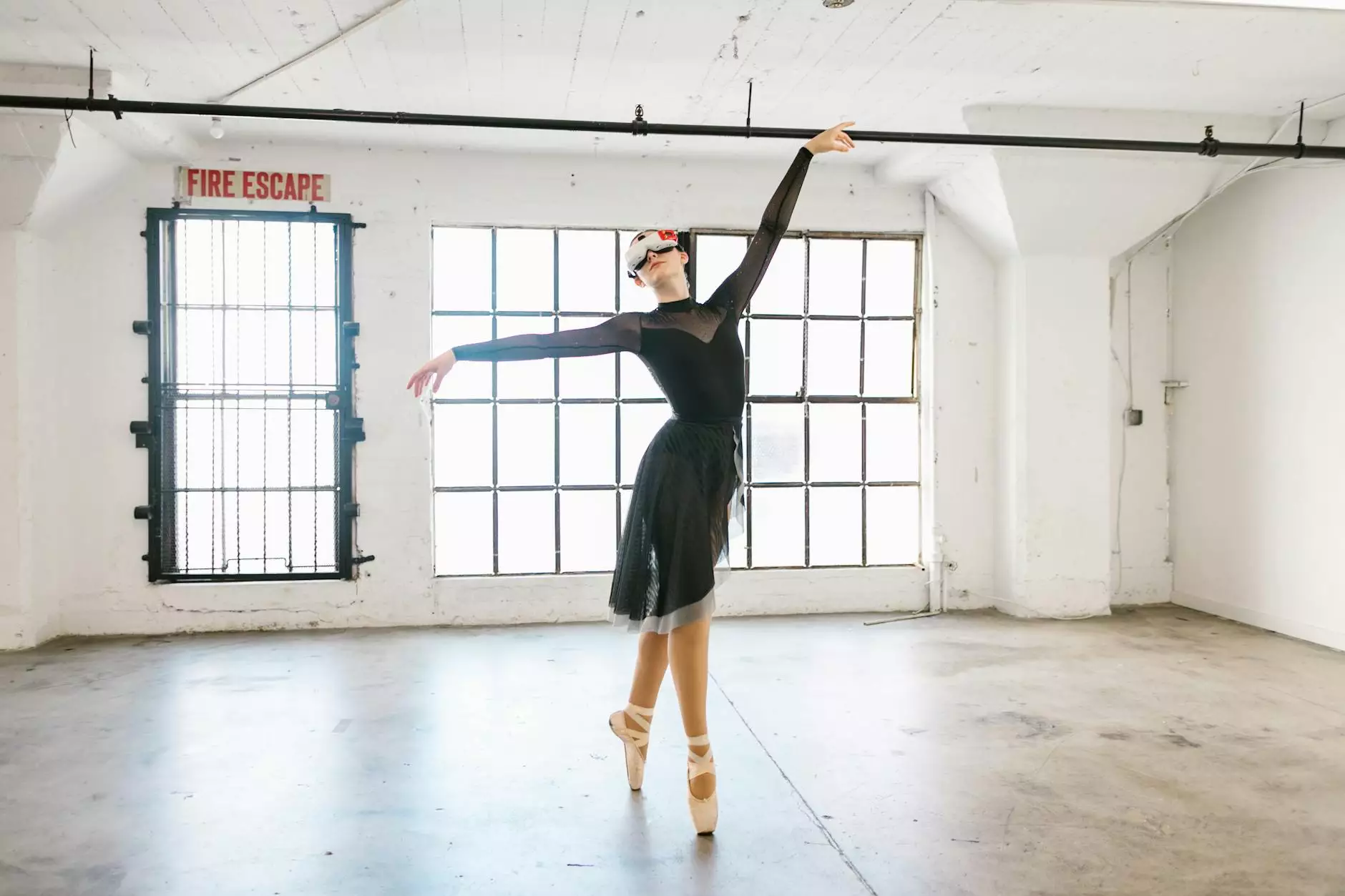
Earthquake simulators play a crucial role in various sectors, particularly in refining and enhancing the capabilities of modern technology like 3D printing. As the demand for innovative solutions in manufacturing continues to rise, understanding the integration of these simulators into current practices can yield significant benefits. This article delves into how earthquake simulators aid in 3D printing, ensuring safety, improving design capabilities, and ultimately leading to advancements in construction and manufacturing.
Understanding Earthquake Simulators
Earthquake simulators are advanced technological tools designed to replicate the effects of seismic activity on structures and materials. By creating controlled environments where buildings and materials can be tested against simulated earthquakes, engineers and researchers can assess performance, durability, and safety. These simulators are invaluable in earthquake-prone areas where the integrity of structures is a primary concern.
The Role of Earthquake Simulators in 3D Printing
The incorporation of earthquake simulators into the realm of 3D printing has opened up new avenues for innovation and safety. Here’s how:
1. Testing Materials and Design Frameworks
One of the primary advantages of integrating earthquake simulators with 3D printing technology is the ability to test various materials and design frameworks under simulated seismic conditions. This thorough testing process allows researchers and developers to:
- Identify weaknesses in printed structures.
- Enhance the overall durability of materials used in 3D printing.
- Develop designs that can withstand significant seismic forces.
Through iterative testing, manufacturers can refine their printing techniques, ensuring that components not only meet design specifications but also adhere to safety standards crucial for earthquake-prone regions.
2. Advancements in Smart Materials
Earthquake simulators enable the exploration of smart materials within the 3D printing spectrum. These materials can adjust their properties in response to stimuli, enhancing resilience during seismic events. Using simulators, researchers can:
- Experiment with shape-memory alloys.
- Test self-healing materials that can repair themselves post-earthquake.
- Investigate composites that combine multiple material properties for improved performance.
The findings gained from these experiments can lead to groundbreaking advancements, promoting greater safety in construction and manufacturing practices.
3. Enhancing Architectural Resilience
For architects and engineers, earthquake simulators provide a pathway to design structures that are inherently more resilient to seismic activity. By incorporating simulator feedback, architects can:
- Create innovative designs that distribute seismic forces more evenly across a structure.
- Utilize 3D printing to fabricate building components optimized for seismic performance.
- Design modular structures that can be easily adapted or relocated in the event of seismic activity.
This proactive approach not only improves safety but also minimizes potential damage during earthquakes, creating a more sustainable environment.
Case Studies: Successful Implementations
Numerous projects have showcased the synergistic effects of combining earthquake simulation with 3D printing technology. Let's explore some notable examples:
Case Study 1: The Resilient Homes Initiative
In a prominent initiative aimed at providing affordable housing in earthquake-prone regions, engineers utilized earthquake simulators to evaluate the architectural integrity of various 3D-printed housing designs. The project successfully:
- Validated design concepts that significantly reduced the risk of structural failure.
- Developed a standardized testing protocol for new materials used in 3D printing.
- Inspired confidence in 3D printing as a viable solution for disaster-resistant housing.
Case Study 2: Smart Seismic Bridges
A high-profile engineering firm integrated earthquake simulators in designing a new class of bridges that incorporate 3D printing. The results showcased innovative approaches such as:
- Dynamic responses to simulated seismic activity, informing adjustments to the structural design.
- Verification of new composite material performance under stress.
- Establishment of new industry standards for bridge safety and design.
Such projects highlight the transformative potential of leveraging both technologies in engineering fields.
The Future of Earthquake Simulation and 3D Printing
Looking forward, the collaboration between earthquake simulators and 3D printing is set to grow stronger. As technology evolves, so too do the strategies engineers can employ, including:
- Artificial intelligence integration for predictive analysis of material performance.
- Enhanced modeling software that simulates the interaction of printed materials and seismic forces accurately.
- Greater collaboration across disciplines, including architecture, engineering, and computer science, to devise comprehensive solutions to construction challenges.
This evolution paves the way for safer structures, reduced environmental impact, and innovations that can ultimately save lives during seismic events.
Conclusion: The Synergy of Earthquake Simulators and 3D Printing
The integration of earthquake simulators with 3D printing technology marks a new era in construction and manufacturing, especially in regions where seismic activity poses a significant risk. As industries continue to adapt and evolve, the potential for innovation is immense. By prioritizing safety and resilience, businesses not only protect their investments but also contribute to the overall well-being of communities worldwide.
At Infotron, we are committed to leveraging the latest technologies to advance the fields of manufacturing and construction, ensuring that our products and solutions are designed with the utmost attention to safety and efficacy. Stay ahead of the curve by embracing the technologies that bring us closer to a safer and more efficient future.