The Evolution of Precision Injection Mould Factories
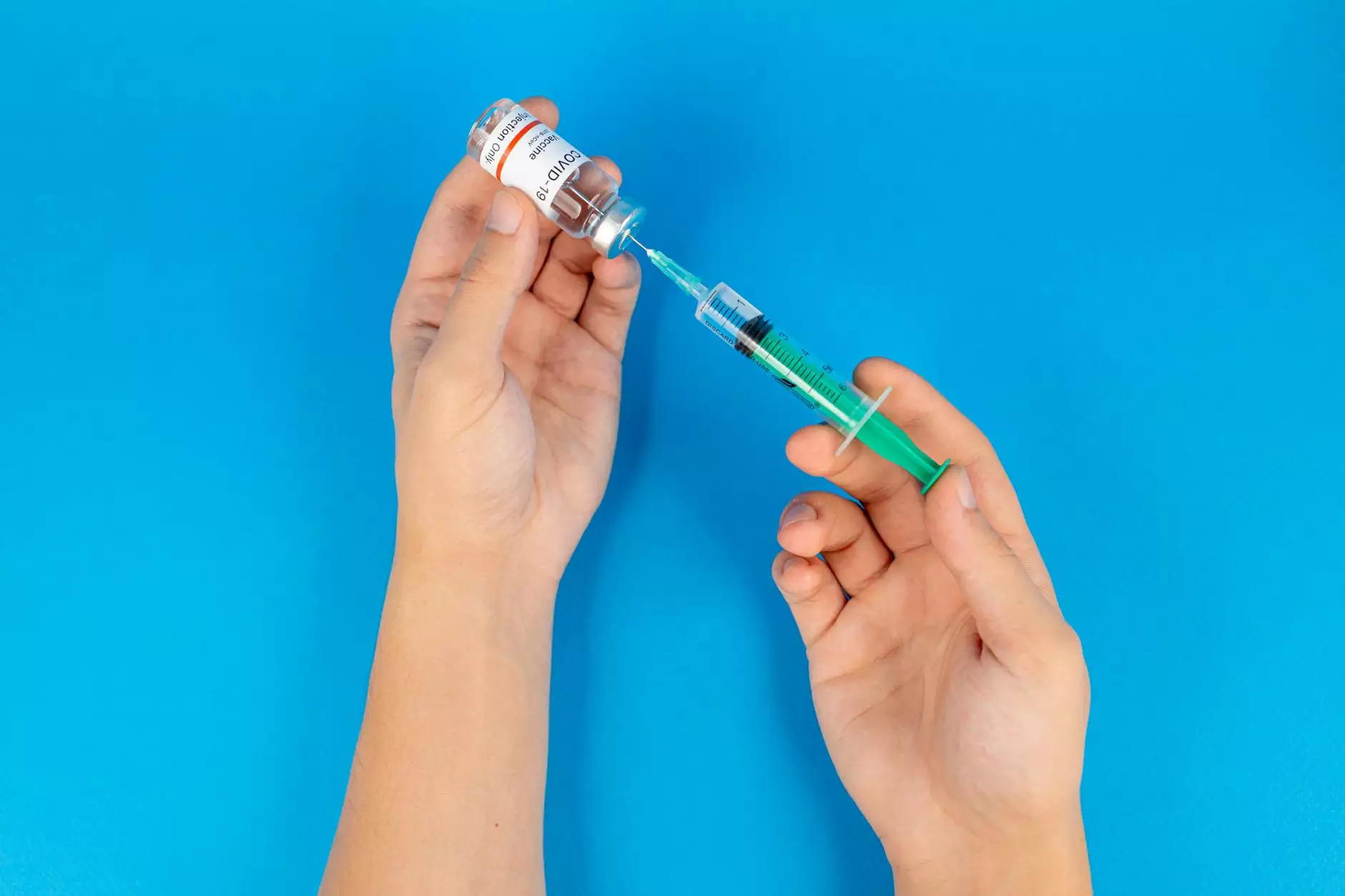
Precision injection mould factories have become the backbone of modern manufacturing, offering unparalleled quality and efficiency. These facilities are essential for producing a wide range of plastic products, components, and assemblies used across various industries, including automotive, medical, consumer goods, and electronics. In this comprehensive guide, we delve deep into what makes a precision injection mould factory a linchpin in manufacturing and how businesses can leverage this technology to enhance productivity and product quality.
1. Understanding Injection Moulding
Injection moulding is a manufacturing process that involves injecting molten material into a mould to shape objects. This technique is extensively used for processing plastic but may also include metals and other materials. The efficiency of this method allows mass production with minimal waste, which enhances sustainability in manufacturing.
1.1 How Injection Moulding Works
At its core, the injection moulding process involves several key stages:
- Material Selection: The choice of material is crucial; common materials include thermoplastics and thermosetting plastics.
- Heating: The selected material is heated until it reaches a molten state.
- Injection: The molten material is injected into a prepared mould.
- Cooling: The injected material is cooled to solidify and take the shape of the mould.
- Demoulding: The finished part is removed from the mould for inspection and packaging.
2. The Advantages of Precision Injection Moulding
Companies investing in a precision injection mould factory enjoy many benefits, including:
- High Precision: The modern machinery used in precision injection moulding ensures that even the tiniest specifications are met.
- Scalability: This process allows for easy scalability; once the mould is created, it can produce thousands of identical parts efficiently.
- Cost-Effectiveness: Although the initial setup cost may be high, the long-term savings due to reduced waste and high production efficiency outweigh the expenses.
- Complex Designs: Precision moulding enables the production of intricate designs and complex geometries that would be impossible to achieve with traditional manufacturing methods.
3. Key Features of a Precision Injection Mould Factory
When searching for a top-tier precision injection mould factory, several crucial features should be considered:
3.1 Advanced Technology
The use of advanced machinery, such as CNC (Computer Numerical Control) machines, ensures precision and repeatability in the manufacturing process. High-speed injection moulding machines also increase efficiency.
3.2 Expertise in Metal Fabrication
As part of the Metal Fabricators category, a precision injection mould factory must have skilled professionals with extensive experience in metal fabrication techniques. This expertise is pivotal for producing high-quality moulds that withstand multiple production cycles.
3.3 Quality Assurance Practices
A reputable factory will implement rigorous quality assurance protocols, including:
- In-Process Inspection: Monitoring the production process to detect deviations in real-time.
- Final Product Testing: Conducting various tests on finished products to ensure they meet all specified tolerances and performance criteria.
- Certifications: Compliance with international quality standards, such as ISO 9001, enhances credibility and reliability.
4. The Role of Materials in Precision Moulding
The choice of material significantly impacts the manufacturing process and the quality of the final product. Common materials used in precision injection moulding include:
- Thermoplastics: Widely used due to their versatility and ability to be remolded. Examples include ABS, polycarbonate, and nylon.
- Thermosetting Plastics: These materials harden permanently after being set, offering high durability and resistance to heat.
- Metals: Some precision moulds utilize metal injection moulding (MIM) to create intricate parts from metal powders.
5. Cost Considerations in Precision Injection Moulding
Cost analysis is critical for businesses considering precision injection moulding. Here are the primary factors affecting costs:
- Tooling Cost: Designing and creating moulds can be expensive, but these costs are spread across a large number of units in mass production.
- Material Costs: The choice of material can influence overall production costs significantly. Choosing high-quality materials can lead to better performance.
- Production Volume: Higher production volumes invariably lower the cost per unit, making detailed market analysis essential for profitability.
6. Sustainability in Precision Injection Moulding
Sustainability is becoming a focal point for modern manufacturers. Precision injection mould factories can adopt practices to minimize their environmental impact, such as:
- Material Efficiency: Utilizing recycled materials where possible to reduce waste.
- Energy Efficiency: Investing in energy-efficient machinery to lower energy consumption.
- Recycling Scraps: Implementing systems to recycle scraps generated during the manufacturing process.
7. The Future of Precision Injection Mould Factories
As technology continues to evolve, the future of precision injection mould factories looks promising. Key trends include:
- Automation: The increasing automation of production processes reduces labor costs and enhances safety.
- 3D Printing Integration: Hybrid systems that combine traditional moulding with 3D printing technology may emerge for rapid prototyping.
- Artificial Intelligence: AI can optimize production processes and maintenance schedules, enhancing efficiency and reducing downtime.
Conclusion
In conclusion, investing in a precision injection mould factory offers numerous advantages for businesses looking to enhance their manufacturing capabilities. With the right technology, expertise, and commitment to quality, companies can produce high-precision components that meet the demands of today's fast-paced markets. As sustainability and technological advancements continue to shape the industry, staying ahead of trends and innovations is essential for enduring success. Explore how our skilled metal fabricators at deepmould.net can elevate your manufacturing processes and deliver exceptional results tailored to your needs.