Understanding LOLER Compliance in South Wales
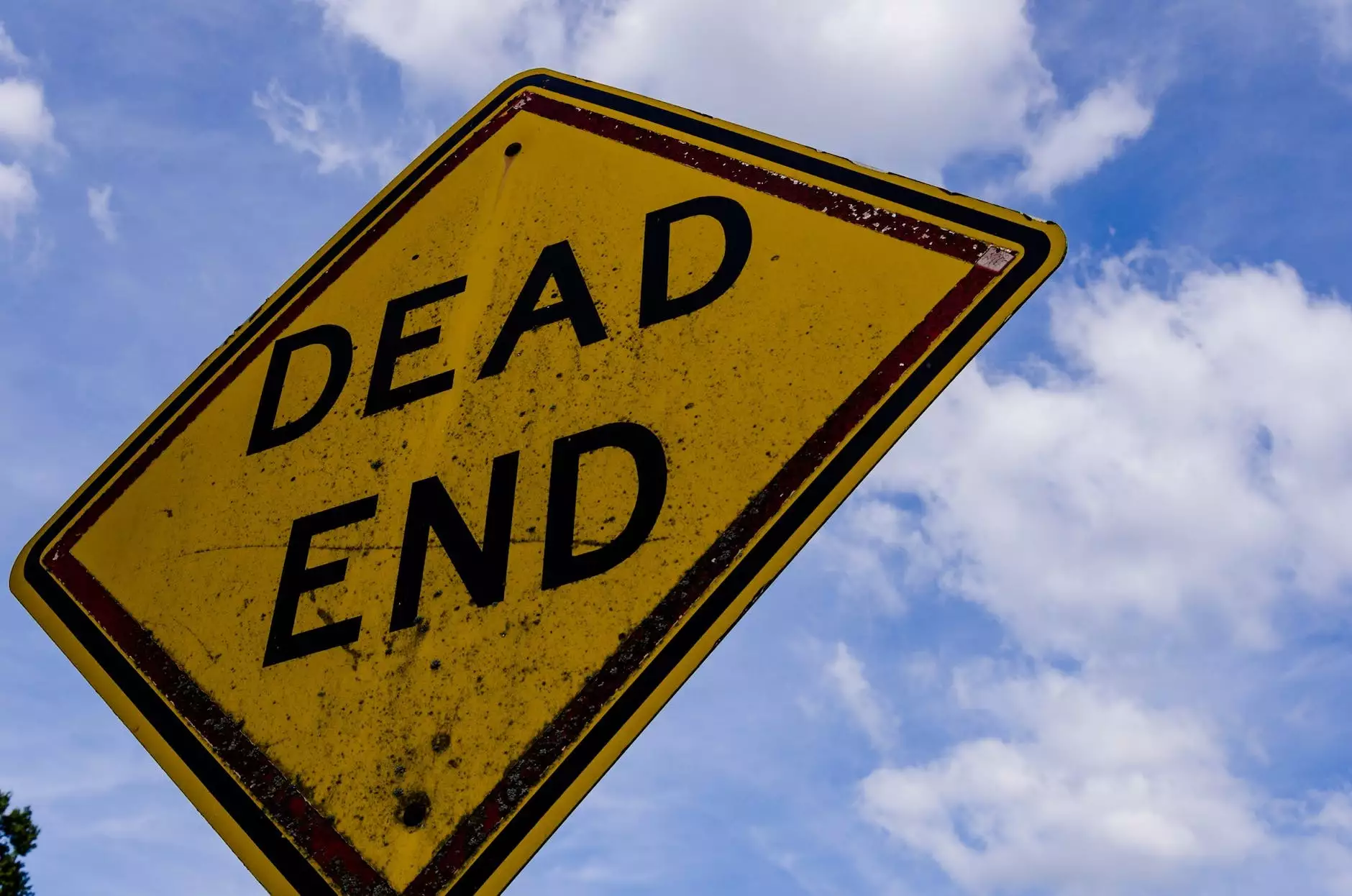
In today’s business environment, particularly for those dealing with lifting equipment and machinery, compliance with health and safety regulations is more critical than ever. One of the key regulations that businesses in South Wales need to adhere to is the Lifting Operations and Lifting Equipment Regulations (LOLER). This regulation is designed to ensure that all lifting operations are carried out safely and efficiently, minimizing the risk of accidents and injuries in the workplace.
What is LOLER?
The Lifting Operations and Lifting Equipment Regulations 1998 (LOLER) require that all lifting equipment used in the workplace is fit for purpose, properly maintained, and regularly inspected. This regulation applies to a wide range of equipment, including cranes, hoists, and lifting accessories. The goal of LOLER is clear: to ensure the safety of employees and the public while using lifting equipment.
The Importance of LOLER Compliance in South Wales
Compliance with LOLER is essential for businesses for several reasons:
- Safety: Primarily, LOLER compliance is crucial for the safety of workers and the public. Properly maintained and inspected lifting equipment reduces the risk of accidents, injuries, and fatalities.
- Legal Obligation: Non-compliance can result in legal repercussions, including fines and other penalties. Businesses must meet LOLER standards to operate legally in South Wales.
- Insurance: Insurance companies may require proof of compliance for coverage. An accident involving non-compliant equipment can lead to claims being denied.
- Reputation: A strong commitment to safety enhances your business’s reputation. Clients and customers are increasingly aware of safety standards and prefer working with compliant organizations.
- Operational Efficiency: Regular maintenance not only keeps your equipment compliant but also ensures that it operates efficiently, reducing downtime and improving productivity.
The Key Components of LOLER Compliance
To achieve LOLER compliance, businesses must focus on several critical components:
1. Thorough Examination
All lifting equipment must undergo a thorough examination by a competent person at least once every 6 months—or more frequently if specified by the manufacturer. This examination checks the equipment's condition and ensures it is fit for use.
2. Regular Inspections
In addition to thorough examinations, regular inspections are necessary to ensure that the equipment remains safe to use. This includes checking for wear and tear, as well as ensuring safety features are functional.
3. Maintenance
Establishing a rigorous maintenance schedule is essential. This should be based on the manufacturer’s recommendations and the equipment's usage. Proper maintenance can prevent failures and extend the life of the equipment.
4. Employee Training
All employees using lifting equipment must receive appropriate training. Educating staff on safe operating procedures and potential risks is vital for achieving a safe working environment.
LOLER Compliance Process
Establishing a LOLER compliance process involves several steps:
- Assessment: Evaluate your lifting equipment to determine what needs to be compliant.
- Documentation: Keep detailed records of all inspections, maintenance work, and training procedures.
- Communication: Ensure that all employees are aware of their responsibilities regarding LOLER compliance.
- Regular Reviews: Periodically review safety and compliance procedures as conditions change or as new equipment is introduced.
SafePlant UK and LOLER Compliance
At SafePlant UK, we understand the complexities surrounding LOLER compliance in South Wales. Our team of experts is dedicated to helping businesses ensure that their lifting operations comply with all relevant legislation. Here’s how we can assist you:
1. Expert Consultations
We offer consultations to assess your current lifting equipment and provide tailored advice on achieving compliance with LOLER regulations.
2. Comprehensive Inspection Services
Our thorough examination services are conducted by qualified inspectors who follow strict protocols to ensure your equipment meets all safety standards.
3. Training Programs
SafePlant UK also provides training for your staff, focusing on safe practices and compliance requirements. Educated operators are key to minimizing risks associated with lifting equipment.
4. Ongoing Support
Compliance is not a one-time affair. We offer continuous support, including re-inspections and updates on regulations, to ensure you remain compliant as your business evolves.
Conclusion
In conclusion, LOLER compliance in South Wales is a vital aspect of operating a safe and effective business involving lifting equipment. Understanding and adhering to these regulations is not only a legal requirement but also a best practice that protects your employees, enhances your reputation, and ensures the efficiency of your operations. At SafePlant UK, we are committed to guiding you through the complexities of compliance, making safety a priority in your workplace.
For more information about our services or to schedule a consultation, visit us at SafePlant UK. Together, we can create a safer working environment for everyone involved.
loler compliance south wales